The excitement of finally putting in a roll bar got to me lol. I’ve read the instructions several times in addition to all the install threads and still managed to mess up.
When bolting the main hoop to the car(3 M8 bolts each side) I ended up cross threading one of the bolts. More specifically the one on the top in relation to the other two. Every other bolt went in smoothly except this one. Didn’t realize it was cross threading. I am able to snug it down but realized the torque spec will be off and I won’t be at peace knowing that with it being a safety device. So the thickness of the threads in which the bolts go into is about 3-4mm. I figured I have a few options.
-Try to chase the threads with a M8 tap and die
-enlargen the hole to a M10 and tap it
- use a M8 nutsert (will have to see what metal thickness the one I have can be used for)
-just continue using the same bolt that caused the cross thread.
I know it’s a silly mistake but I rather ask more knowledgeable people than pay a serious price.
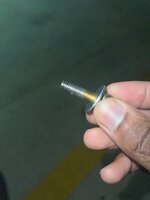
When bolting the main hoop to the car(3 M8 bolts each side) I ended up cross threading one of the bolts. More specifically the one on the top in relation to the other two. Every other bolt went in smoothly except this one. Didn’t realize it was cross threading. I am able to snug it down but realized the torque spec will be off and I won’t be at peace knowing that with it being a safety device. So the thickness of the threads in which the bolts go into is about 3-4mm. I figured I have a few options.
-Try to chase the threads with a M8 tap and die
-enlargen the hole to a M10 and tap it
- use a M8 nutsert (will have to see what metal thickness the one I have can be used for)
-just continue using the same bolt that caused the cross thread.
I know it’s a silly mistake but I rather ask more knowledgeable people than pay a serious price.
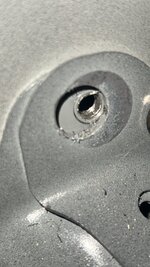
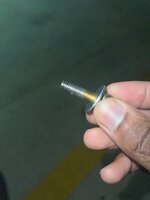