- 16
- 4
2014 Mustang GT, 86,000 miles.
About a year ago I started to feel the rear of the car steer under braking. I swapped out my rear LCAs for J&M tubular LCAs with the rotoball rubber/poly bushings.
When I went to remove the OEM LCAs driver's side body end bushing crush tube was seized to the lca bolt. I ended up destroying the bushing before limping the car to a dealership to have the old bolt cut out. I fear they may have damaged the torque box then, but I didn't have any trouble all year with the J&M LCAs, so i put it out of my mind.
This past Friday i start getting a good clunk under hard braking and in reverse from the same torque box, along with the same rear steer sensation. I get the car on a lift today and it turns out the inner bolt hole has ovaled and the bolt is moving around under power and braking.
The shop said I can weld in a plate and drill a new hole. I have concerns about proper alignment if I do this.
I see that Lakewood Engineering sells a torque box brace which you weld in and bolt through. Is this a viable alternative or would they not be strong enough to bear the longitudinal loads?
Sent from my SAMSUNG-SM-G890A using Tapatalk
About a year ago I started to feel the rear of the car steer under braking. I swapped out my rear LCAs for J&M tubular LCAs with the rotoball rubber/poly bushings.
When I went to remove the OEM LCAs driver's side body end bushing crush tube was seized to the lca bolt. I ended up destroying the bushing before limping the car to a dealership to have the old bolt cut out. I fear they may have damaged the torque box then, but I didn't have any trouble all year with the J&M LCAs, so i put it out of my mind.
This past Friday i start getting a good clunk under hard braking and in reverse from the same torque box, along with the same rear steer sensation. I get the car on a lift today and it turns out the inner bolt hole has ovaled and the bolt is moving around under power and braking.
![20171204_112154[1].jpg 20171204_112154[1].jpg](https://trackmustangsonline.com/data/attachments/2/2780-452968767ef13de46433579e6fa147df.jpg)
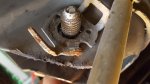
The shop said I can weld in a plate and drill a new hole. I have concerns about proper alignment if I do this.
I see that Lakewood Engineering sells a torque box brace which you weld in and bolt through. Is this a viable alternative or would they not be strong enough to bear the longitudinal loads?
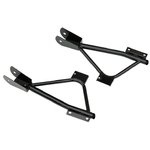
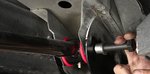
Sent from my SAMSUNG-SM-G890A using Tapatalk
Last edited: